Understanding Production Costs: A Detailed Analysis
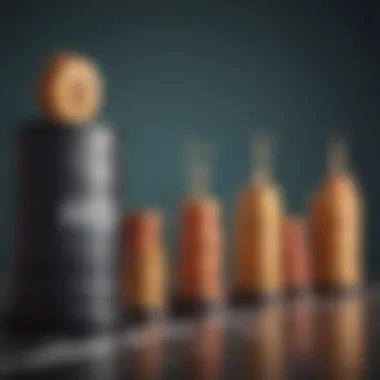
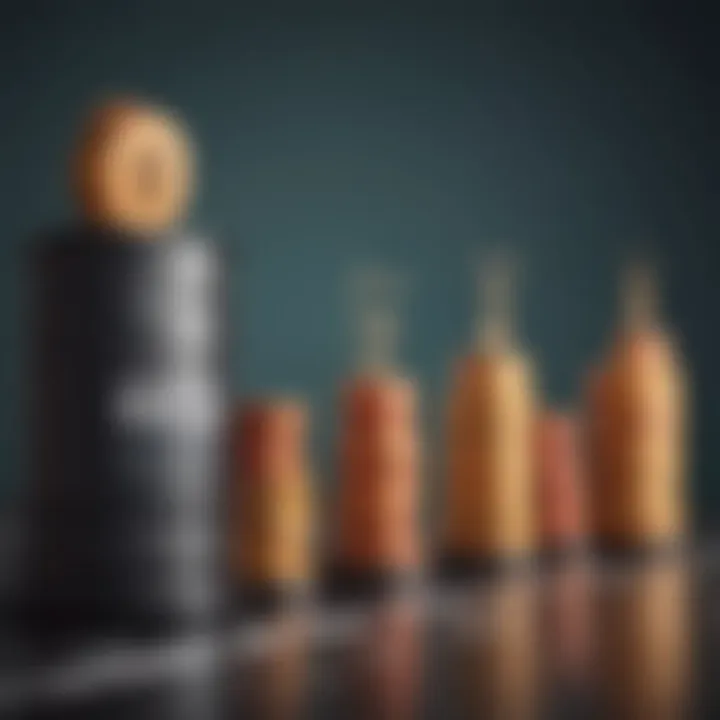
Intro
Understanding production costs is not just a financial exercise; itās a fundamental aspect of running a sustainable and profitable business. Whether one is in manufacturing, services, or even in creative industries, knowing the nitty-gritty of costs can make or break a venture. This knowledge allows for sharper decision-making, prudent budgeting, and maximizing profitability.
Production costs consist of diverse elements, all woven together to form the backbone of financial analysis. When examining these costs, one often encounters terms like fixed costs, variable costs, direct costs, and indirect costs. Each of these terms represents a piece of the financial puzzle that, when put together, highlights how resources are utilized, how products are priced, and ultimately, how profits are generated.
For investors, this understanding is paramount. Ignoring production costs can lead to overestimating potential profits and, in turn, poor investment decisions. Therefore, a comprehensive approach to analyzing these costs will not only shed light on a company's operational efficiency but also help in identifying potential areas for improvement.
In this article, we will specifically dive into the intricacies of production costs. We will break down the essential components, provide methodologies for calculation, and integrate practical examples to emphasize how these concepts translate into real-world scenarios. By the end of this exploration, readers should feel equipped to assess production costs with confidence, make informed investment choices, and understand how these costs impact overall financial decision-making.
Intro to Production Costs
Understanding production costs is a cornerstone of effective business strategy. At the heart of every successful operation, knowing how to dissect these costs is not just a luxury; it's a necessity. In this section, we will explore the key components of production costs, shining a light on their definitions, importance, and fallout in the realms of business and investment.
Defining Production Costs
Production costs are the total expenses incurred in the manufacturing of goods or services. This broad category can be segmented into several distinct types, allowing for a more meticulous analysis. Here are some primary elements embedded in production costs:
- Material Costs: These encompass the raw materials needed to create a product. Think about wood for furniture or steel for machinery. The price can fluctuate based on market demands.
- Labor Costs: This refers to wages paid to employees directly involved in production. So, if an assembly line requires ten workers, their combined salaries impact the overall cost.
- Overhead Costs: This collection includes fixed costs related to the operation that doesn't directly tie to production, such as utilities, rent, and equipment depreciation.
Being clear about these definitions sets the stage for deeper discussions. When an investor evaluates a company, understanding its production costs can reveal much about its operational efficiency and profit margins.
Importance in Business and Investment
Production costs wield significant influence over a business's financial health. For decision-makers, these costs determine pricing strategies and influence profit margins. Hereās why they matter:
- Pricing Decisions: Businesses must cover production costs while setting their pricing. If production costs rise and prices do not adjust, profitability is at risk.
- Investment Evaluation: Investors are keenly interested in production costs as they gauge the sustainability of profit margins. A company with well-controlled costs is often more attractive than one without.
- Efficiency Indicators: Monitoring production costs can reveal areas where a business may be overspending, thus allowing for strategic adjustments and operational enhancements.
- Market Competitiveness: Understanding the cost structure allows businesses to stay competitive. If a company can produce at a lower cost than market competitors, it can capture greater market share.
"Effective management of production costs is not just about reducing expenses; it's about making informed decisions that drive business growth."
In summary, the importance of production costs cannot be overstated. They are more than mere numbers on a balance sheet; they are vital indicators of overall business health and potential investment returns. As we continue through this article, keep these foundational concepts in mind as they will serve as the bedrock for understanding the complexities of production costs.
Component Breakdown of Production Costs
Understanding the breakdown of production costs is crucial for anyone serious about financial management. This segment sheds light on the specific elements that make up production expenses, allowing businesses to strategize effectively. A clear breakdown helps in identifying potential areas for cost reduction and efficiency improvement, which ultimately leads to better profit margins. Knowing the components can aid investors and financial advisors in making more informed decisions, enhancing their overall financial strategies.
Fixed Costs
Definition of Fixed Costs
Fixed costs are the expenses that do not fluctuate with the level of production or sales activity. These are costs that a business must pay regardless of its operational performance. Think of rent, salaries, and insurance ā these expenses remain constant over a specific period. The key characteristic of fixed costs is their stability; businesses can plan their finances more effectively when they know there are certain costs that will not vary month-to-month. However, while these are predictable, they can also represent a burden during periods of low revenue.
Examples of Fixed Costs
Examples of fixed costs include salaries of permanent staff, rent for facilities, and depreciation of fixed assets. For instance, if a company pays $3,000 for office rent each month, that expense remains unchanged whether they produce 100 units or 1,000 units. This predictability is beneficial for planning budgets, but it can be a double-edged sword; if production falls significantly, the fixed costs can squeeze profit margins tighter than it would be with variable costs, which adjust according to production levels.
Impact on Overall Expenses
The impact of fixed costs on overall expenses is significant. They make up a substantial portion of a companyās total costs. A high ratio of fixed costs can lead to financial strain, especially during downturns in business activity. This rigidity can lead to suboptimal decision-making because thereās less flexibility to adapt to market conditions. On the flip side, the stability of fixed costs offers predictability in financial forecasting, which is essential for informed strategic decisions.
Variable Costs
Definition of Variable Costs
Variable costs are expenses that change in direct correlation to the production volume. This means that if a business produces more goods, its variable costs, such as materials and labor, will increase. This relationship allows companies to manage expenses dynamically; unlike fixed costs, they can reduce their spending during slower production periods. It's this flexibility that makes variable costs an essential component in managing production effectively.
Examples of Variable Costs
Some common examples of variable costs include raw materials, shipping expenses, and direct labor costs. For example, if a bakery uses flour for its products, the cost of flour will increase with the number of loaves baked. This characteristic allows businesses to maintain tighter control over their financials during fluctuations in sales. However, heavy reliance on variable costs requires active monitoring to avoid unexpected spikes that can affect profit margins.
Correlation with Production Volume
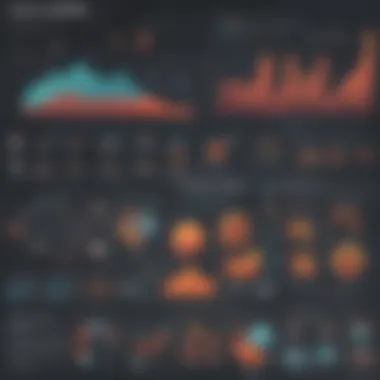
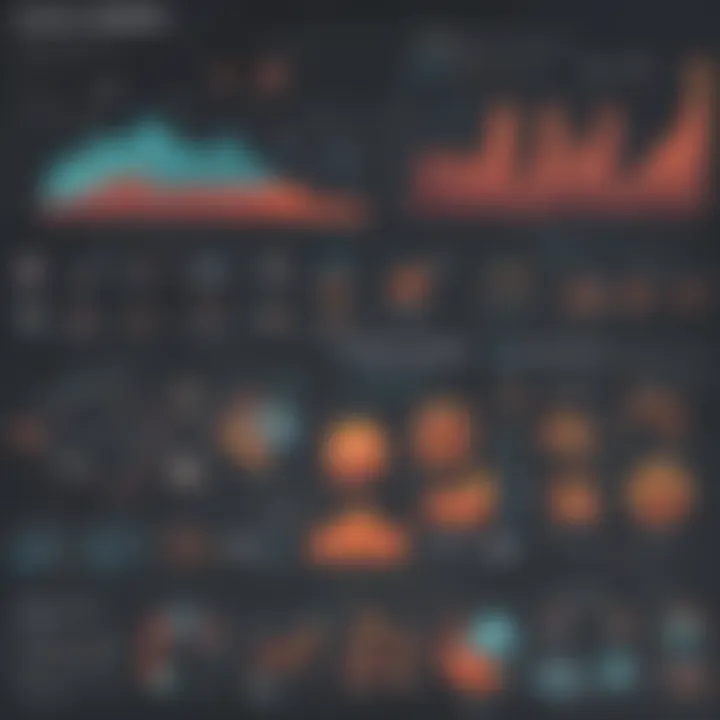
The correlation between variable costs and production volume is straightforward: more production equals higher costs. This relationship allows businesses to plan their finances more dynamically. If a firm predicts a sales increase, it can prepare for increased raw material costs ahead of time. However, if production scales too quickly without proper cost management, it can result in financial strain. Understanding where the tipping point lies between profitability and variable costs is critical for stakeholders in strategic planning.
Semi-Variable Costs
Understanding Semi-Variable Costs
Semi-variable costs, also known as semi-fixed costs, exhibit both fixed and variable characteristics. They contain a component that stays constant regardless of production levels, along with a variable portion that fluctuates with the level of activity. An often-cited example includes utility costsāthere's typically a base charge thatās fixed, while usage drives variable charges. The dual nature of semi-variable costs can complicate forecasting. However, recognizing these costs enables businesses to fine-tune budgeting, making it possible to manage both components effectively.
Examples and Applications
Examples of semi-variable costs include phone bills, which may have a base charge plus additional fees for usage above a certain threshold, and factory maintenance costs, which might include fixed labor charges plus variable costs linked to machine operation. By understanding these examples, businesses can better allocate resources and establish accurate budgets that reflect both the stable and fluctuating aspects of their production costs. The unique feature here is flexibility; with a clear grasp of how these costs function, businesses can develop strategies that make the most out of both fixed and variable aspects.
Calculating Production Costs
When it comes to running a business, understanding how to calculate production costs is like having the secret sauce in your recipe. Itās essential for anyone looking to navigate financial waters effectively. Knowing what goes into the production cost equation helps you pinpoint where money is being spent and where savings can be made. This section shines a light on various methods and common formulas that simplify this often daunting task. With clear steps and practical tools, calculating production costs is more than just number crunching; itās about smart financial planning.
Methods of Calculation
Total Cost Method
The Total Cost Method offers a comprehensive view, factoring in all costs associated with producing goods or services. What makes this approach particularly attractive is its ability to generate a clear picture of overall expenses. Think of total cost as the big canvas where every brushstroke, or expense, matters. It neatly combines both fixed and variable costs, effectively laying out the groundwork for decision-making.
One key characteristic of this method is its straightforward calculation. You simply add fixed costsāthose costs that stay the same regardless of outputāto variable costs, which fluctuate with production levels. This method is favored because it provides clarity on how resources are allocated and helps identify areas of potential savings.
However, itās not all sunshine and rainbows. One downside to the Total Cost Method is that it may not reflect costs accurately at varying output levels, leading to possible misjudgment in pricing strategies. Hence, it might require deeper analysis and adjustments to maintain accuracy as production scales.
Average Cost Method
The Average Cost Method, on the other hand, refines your understanding of production costs by spreading total costs across the units produced. Imagine sitting down with a pie and dividing it equally among friendsāthatās precisely what this method does with costs. Its beauty lies in its simplicity and its ability to provide insights into cost management.
A standout feature here is the way it enables businesses to strike a balance between production volume and profitability. By averaging costs, companies can draft more precise pricing strategies, catering to both the market and their profit goals. This method is particularly helpful in industries where production scales are significant.
Yet, like all good things, it has its challenges. If production volume varies significantly, relying solely on an average can give a skewed perspective, and decisions based on this might lead to profit erosion. Thus, while the Average Cost Method is widely adopted, itās crucial to keep an eye on context and external factors as well.
Common Formulas
Cost Per Unit Formula
Next up is the Cost Per Unit Formula. This formula is like having a trusty calculator that tells you exactly how much youāre spending on each individual unit produced. Calculating the cost per unit allows businesses to measure efficiency and identify when costs might be creeping beyond reasonable limits.
One prominent benefit of this formula is its straightforward application: simply divide the total production costs by the number of units produced. Itās favored because it gives businesses a clear understanding of their operational efficiency. Companies can pinpoint which areas are cost-effective and which need re-evaluation.
However, one should always tread carefully. Sometimes, focusing too heavily on reducing the cost per unit may lead to neglecting other important factors like quality or customer service. So while this formula is a valuable tool, it needs to be used within a deeper context of overall business strategy.
Break-Even Formula
Lastly, we have the Break-Even Formula, a crucial piece of the puzzle for any investor or business owner looking to gauge financial health. It helps determine when total revenue matches total costs, revealing when a business starts turning a profit. This is vital when setting pricing strategies and assessing potential growth.
The Break-Even Formula is advantageous because it provides clarity on the minimum sales necessary to cover costs. With a simple calculationāfixed costs divided by the selling price per unit minus the variable cost per unitācompanies can visualize their financial landscape effectively. This straight talk about profit and loss is what makes this formula stand out.
On the flip side, focusing solely on break-even can lead to oversimplification. It doesnāt account for factors like market dynamics or changes in consumer behavior. So while itās a key indicator of financial health, it ought to be considered alongside other factors for a rounded perspective.
"Understanding production cost calculations underpins effective financial management; itās not merely an exercise in accounting but a vital aspect of strategic decision-making."
In wrapping up this section, realizing the nuances of calculating production costs is crucial for any investor, financial advisor, or analyst looking to deepen their understanding of the underlying mechanics in production management.
Case Studies: Real-world Examples of Production Costs
Examining real-world cases illuminates the often abstract concept of production costs. By diving into actual scenarios, businesses and investors can gain valuable insights, witnessing firsthand how theoretical principles are put into practice. Case studies provide a tangible understanding of cost structures and demonstrate the pragmatic implications of financial decisions. These examples serve not only to showcase various industries but also to underline the unique challenges each faces regarding production costs.
Manufacturing Industry Case Study

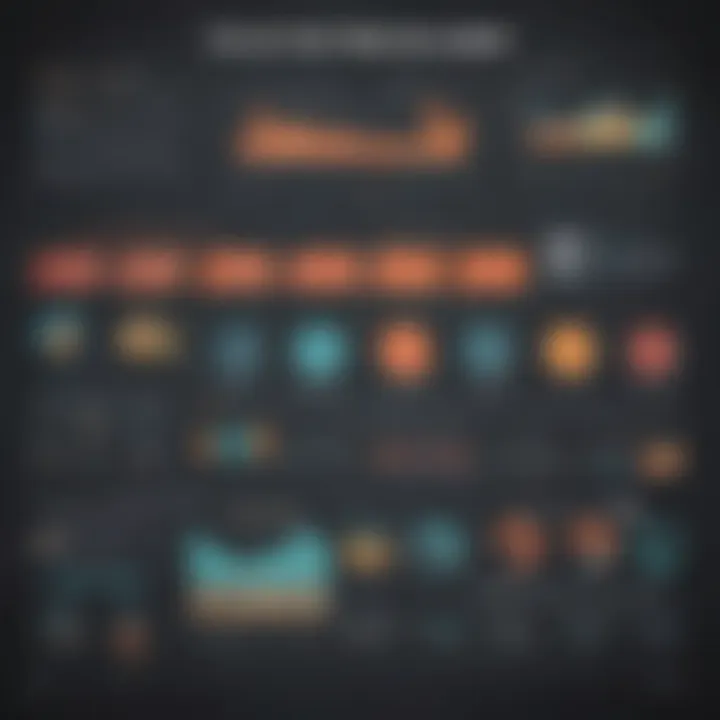
Analysis of Cost Structures
Cost structures in manufacturing are intricate and demand careful scrutiny. At the core, this analysis involves assessing both fixed and variable costs associated with production. For instance, a company like General Motors allocates substantial funds to machinery and labor, which shape their fixed cost base. This makes looking at their cost structure essential.
The standout feature of analyzing these structures is its ability to reveal which costs are controllable versus which are fixed. Understanding this distinction aids companies in refining their budgeting processes. The undeniable advantage of such an analysis is that it enables manufacturers to identify inefficiencies and thus optimize their operations. However, itās not without its downsides; focusing too heavily on cost can sometimes stifle innovation.
Outcomes of Cost Management
When effective cost management strategies are implemented, manufacturers can see a considerable boost in profitability. For example, Toyota's lean manufacturing model emphasizes waste reduction and efficiency, resulting in significant cost savings. The key characteristic of these outcomes is their direct impact on the bottom line; companies that apply rigorous cost management can enjoy higher profit margins, even in competitive markets.
The unique feature of cost management in manufacturing is its adaptability. Different strategies like just-in-time production have particular advantages, making them especially suitable in fast-paced industries. Nevertheless, while these strategies enhance flexibility, they can also lead to vulnerabilities, such as supply chain disruptions. Hence, striking a balance is crucial.
Service Industry Case Study
Cost Considerations in Service Delivery
In the service industry, cost considerations pivot significantly around labor and operational expenses. For example, a company like Starbucks manages costs by optimizing employee schedules and training, leading to enhanced service delivery while controlling labor costs. The unique aspect here lies in how service providers measure performance against their expense structures, protecting profit margins while ensuring customer satisfaction.
Such considerations are critical because they pinpoint how service quality correlates with production costs. While investing in skills and training can elevate service standards, these expenses must align with revenue expectations to avoid diluting profit.
Implications for Profit Margins
The implications of understanding cost structures in the service sector extend beyond simple budgeting. They encompass how pricing strategies are formulated, reflecting both service quality and cost control. Notably, businesses need to track their service delivery costs closely to avoid underpricing or overpricing, which can erode profit margins.
An important characteristic of these implications is that they demand ongoing refinement. In this sector, market conditions shift quickly, affecting both supply and demand. Hence, while certain cost structures provide stability, they also require regular review to maintain profitability. Companies that fail to adapt may find their margins squeezed, making vigilance in cost management imperative.
In sum, case studies on production costs, whether in manufacturing or service industries, serve as rich grounds for understanding the nuanced dynamics of expense management. These insights not only guide strategic planning but also shape how organizations pivot in response to financial challenges.
The Relationship Between Production Costs and Pricing Strategies
Understanding the interplay between production costs and pricing strategies is vital for any organization aiming to thrive in a competitive market. Companies not only need to cover their expenses but also ensure they achieve profit margins that sustain them in the long run. When production costs are well understood, businesses can set prices that pivot effectively on both the cost and value delivered to consumers.
A detailed grasp of how production costs relate to pricing strategies allows investors and financial decision-makers to forecast profitability better and strategies for growth. This aspect sheds light on numerous considerations, including consumer psychology, competitive positioning, and market dynamics. By analyzing these factors, businesses can fine-tune their pricing to reflect not only their costs but also the perceived value in the eyes of their customers.
Influence on Market Pricing
The relationship between production costs and market pricing often fluctuates based on various factors. Companies must consider how fixed, variable, and semi-variable costs can shape their pricing strategies. For instance, in an inflationary economy, rising production costs may compel firms to adjust prices upwards, which can be a double-edged sword.
- Cost-Plus Pricing: This method involves adding a standard markup to the cost of production. While straightforward, it can lead to prices that ignore market conditions.
- Value-Based Pricing: This strategy considers the perceived value to the consumer rather than just the product cost. By aligning price with customer value, businesses can potentially maintain profit margins even if production costs rise.
Effective pricing strategies often balance these influences, ensuring that businesses remain competitive while still covering their costs. Understanding production costs gives management a tool to cost-effectively play the pricing game, maximizing revenue without jeopardizing market share.
Strategies for Cost Management
Minimizing Costs
Minimizing costs is a cornerstone of many pricing strategies and aims directly at enhancing profitability. The key characteristic of this approach is its focus on reducing waste and improving operational efficiencies. By scrutinizing and streamlining processes, companies can lower production costs and, consequently, set more competitive prices.
A unique feature of minimizing costs is the implementation of lean manufacturing techniques, which emphasize the removal of non-value-added activities. This not only reduces costs but often improves production quality as well. However, itās crucial to recognize that overly aggressive cost-cutting can sometimes lead to diminished product quality or employee morale, which can backfire in the long run.
Maximizing Efficiency
Maximizing efficiency extends beyond simply minimizing costs; it emphasizes getting the most out of every resource. This can involve adopting new technologies, improving workflows, or investing in employee training. The key characteristic of maximizing efficiency is that it not only lowers costs but also enhances productivity and quality of output.
One noteworthy aspect of maximizing efficiency is its focus on proactive resource management, which can shield companies from sudden spikes in production costs. However, striking the perfect balance can be tricky, as investments in efficiency might require substantial upfront costs, which may not pay off immediately.
"Understanding the relationship between production costs and pricing strategies is not just about saving money; it's about strategically navigating the marketplace to deliver value while maintaining profitability."
Role of Technology in Reducing Production Costs
In todayās fast-paced business environment, the role of technology in reducing production costs is paramount. Companies are increasingly recognizing the impacts that innovative tech solutions can have on their operational efficiencies. Whether itās through automating processes or leveraging data analysis, technology provides a pathway to observe and manage costs more effectively than ever before.
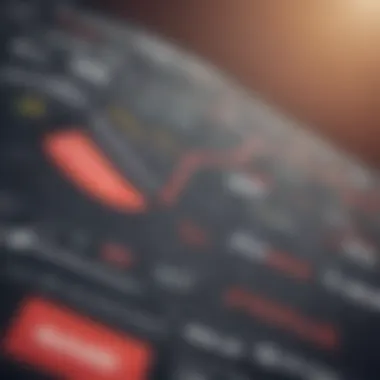
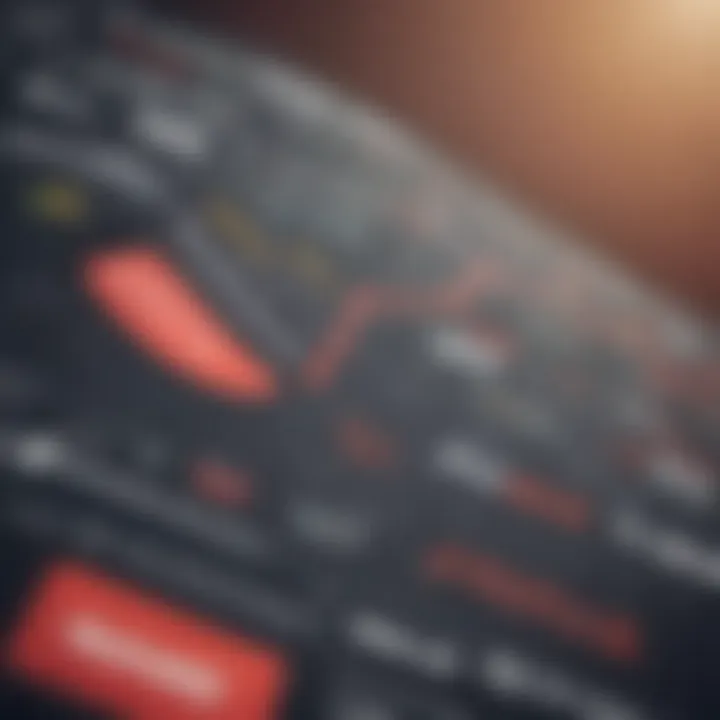
When we talk about reducing production costs, we mean any means of optimizing resources, improving speed, and enhancing consistency. Investors and financial advisors should note that the implementation of technology often leads to substantial savings, allowing businesses to allocate funds more judiciously. Letās break this down further into automation and data analysis.
Automation in Production
Automation has become the backbone of modern industrial processes. By using machines and software to perform tasks that once required human intervention, businesses streamline their production. This shift has led to several benefits, including:
- Increased Efficiency: Machines can operate continuously without breaks, significantly boosting output compared to human labor.
- Improved Accuracy: Automated systems reduce human error, thus maintaining product quality and minimizing waste.
- Lower Labor Costs: Automation can lead to a reduction in the workforce needed for repetitive tasks, which can, in turn, reduce payroll expenses.
For example, consider an automotive manufacturer that adopts robotic assembly lines. These robots not only assemble parts swiftly but also ensure a level of precision that can be hard to achieve manually.
"Automation paves the way towards not just cutting costs, but also scaling operations with much fewer resources."
However, it's worth noting that investing in automation requires initial capital and entails a learning curve. It must be strategically managed to avoid pitfalls like underutilization of new technology.
Data Analysis and Resource Allocation
Data analysis has emerged as a critical component in managing production costs. By harnessing vast amounts of data, companies can make informed decisions that influence their financial outcomes. Key elements of this trend include:
- Cost Tracking: Analyzing where costs are incurred allows businesses to pinpoint inefficiencies.
- Supply Chain Optimization: With advanced analytics, companies can forecast demand and adjust their supply-chain strategy accordingly, minimizing excess inventory.
- Resource Allocation: By understanding performance metrics, firms can allocate resources more effectively, focusing efforts where they yield the highest returns.
The use of software tools and platforms that analyze production data is becoming more common. Businesses utilizing these tools not only enhance operational clarity but often discover cost-saving opportunities they may have never considered. For example, a coffee manufacturer might analyze consumer buying patterns to determine optimal production schedules, preventing overproduction and waste.
Future Trends in Production Cost Management
In a rapidly evolving economic climate, understanding the future trends in production cost management is crucial for any investor or financial analyst. As businesses strive to adapt to increasing competition and shifting consumer demands, recognizing these trends can prove invaluable in making informed decisions. Efficiency takes center stage as companies seek not only to cut costs but also enhance productivity without sacrificing quality. This balance becomes even more vital as we progress into an era marked by sustainability and globalization.
Sustainability and Cost Efficiency
The integration of sustainability into production cost management strategies is no longer optional, but rather a necessity. Companies are increasingly recognizing that sustainable practices can lead to both cost savings and enhanced brand reputation. The environmental aspect is closely tied to financial performance. By reducing waste, optimizing resource use, and shortening supply chains, businesses can see significant reductions in variable costs.
"Adopting sustainable practices not only meets consumer demands but also contributes to the bottom line."
Key Elements of Sustainability in Cost Management:
- Waste Reduction: Efficient waste management practices can lower material costs significantly.
- Energy Efficiency: Utilizing renewable energy sources leads to lower energy bills over the long haul.
- Eco-friendly Materials: Selecting sustainable materials may have a higher upfront cost but can result in substantial savings in disposal and recycling costs.
The benefits of sustainability are clear. Investors may find companies that prioritize these practices more attractive, as they are likely to be more resilient and adaptive to regulatory changes. Financial advisors should pay close attention to sustainability reports, as these could signal a company's commitment to cost efficiency.
Globalization and Supply Chain Dynamics
The landscape of production costs is heavily influenced by globalization. Companies are no longer restricted to local suppliers or markets. This increased connectivity brings about both challenges and opportunities. For instance, fluctuating exchange rates and geopolitical tensions require companies to adopt versatile and agile supply chain strategies to mitigate risks.
Factors to Consider in Global Supply Chains:
- Diverse Sourcing: Many firms explore multiple sourcing options to ensure the best pricing and quality, which can help lower overall production costs.
- Geopolitical Risks: Businesses must assess political stability in sourcing regions, as disruptions can result in increased expenses.
- Technology and Communication: Streamlining communication within global supply chains can improve efficiency and reduce delays, thus controlling costs.
The current trends highlight that understanding global dynamics is vital for effective production cost management. For a sharper competitive edge, investors and financial analysts should look at how well a company navigates these complexities in its financial planning and forecasting.
In summary, the landscape of production costs is evolving, with sustainability and globalization at the forefront. For investors and analysts, grasping these trends can enhance strategic decision-making and contribute to the broader goal of efficient financial planning.
Culmination
In this article, we have traversed the intricate landscape of production costs, laying bare the essential components that influence financial decisions. Understanding production costs is not merely an academic exercise; it informs practical choices for businesses seeking profitability and sustainability.
As we wrap up our discussion, it is crucial to highlight a few key insights derived from our comprehensive exploration. First, we defined production costs and delved into their significant role in business operations. We broke these costs down into fixed, variable, and semi-variable categories, elucidating how each type impacts overall financial health.
Summarizing Key Insights
- Fixed Costs: These are costs that remain constant regardless of production levels, such as rent and salaries. Their predictable nature allows businesses to plan budgets but can burden finances if not managed wisely.
- Variable Costs: In contrast, these costs fluctuate based on production volume. Understanding this relationship enables firms to optimize production strategies.
- Semi-Variable Costs: This category bridges the gap between fixed and variable costs, influencing planning and forecasting.
- Calculation Methods: We discussed various calculation methodologies, emphasizing the Total Cost and Average Cost methods. Grasping these methods is critical for accurate budgeting.
- Real-world Case Studies: Analyzing manufacturing and service industries provided valuable insights into the practical implications of cost structures, guiding future decision-making.
As the business landscape evolves, staying attuned to production costs is an ongoing necessity.
Implications for Future Financial Planning
The implications of understanding production costs extend well beyond immediate budgeting. For investors and financial advisors, a thorough grasp of these costs enables informed decision-making, better risk assessment, and strategic investment planning.
- Budget Flexibility: This understanding allows businesses to allocate resources more efficiently, establishing financial buffers for periods of fluctuation.
- Profit Margin Optimization: Companies that effectively manage costs can enhance their profit margins, making them more attractive to potential investors.
- Strategic Pricing: Cost knowledge aligns closely with pricing strategies, facilitating competitive positioning in the market.
- Risk Management: Recognizing how costs behave under varying conditions can help anticipate market shocks and plan accordingly.
Ultimately, a deep comprehension of production costs is integral for future financial planning. It empowers businesses to adapt to changes, seize opportunities for efficiency, and lay a stronger foundation for growth. This strategic approach leads to not only enhanced financial performance but also a sustainable business model that can thrive amidst evolving market dynamics.